How is a Roulette Wheel Made?
The process of crafting a roulette wheel is more complex than one may think (perhaps not as physically demanding for an online casino).
There are a variety of games that bring life to any casino floor, from table games to slot machines, players have an abundance of thrilling options to choose from. One of the most popular is clearly Roulette, as plenty of patrons are always seen crowded around its fast-spinning wheel, eager to see where exactly that small white ball will come to a halt. While wrapped up in this anxious anticipation, you’ve probably never considered how the Roulette wheel you play with actually came to be.
However, like all other titles inside a casino establishment, an intricate process of manufacturing gives the games you know and love their final polished look and feel. Read on to learn how Roulette’s most central component, the ‘little wheel’, is crafted.
Roulette Wheel – From Wooden Frame to Metal Handle
Roulette players know that there are two main wheel versions: the French Roulette wheel and the American Roulette wheel, with the latter containing one extra 00 green slot along with the standard red and black alternating fields. With both variants, there are two major parts used in assembly: a static bowl and a wheelhead.
The bowl, or wooden frame (typically 32 inches in diameter), is produced by sanding and polishing wood, with mahogany being the most common material in premium wheels. Textures and edges must look and feel smooth, as the wood’s purpose, alongside its sturdy quality, is to give the wheel a sophisticated, vintage appearance that compliments its historical origins. Although the bowl used in casinos is normally made of wood, its internal elements are produced with plastic materials.
After the frame has been made, a ball track and lower ball track apron equipped with ball deflectors and a special wheelhead-supporting spindle is inserted into the bowl. Then the wheelhead is settled inside carefully, clicking into place evenly so that it can spin effectively.
The wheelhead’s outer edges is what contains the coloured pockets and numbers where the ball eventually lands. At the surface of the wheelhead is the cone which essentially directs the ball towards a pocket when it is thrown onto the wheel. Last but not least, to hide the inner mechanism, a metal handle called a turret is placed atop the cone, bringing everything together in a decorate, stylish way.
What About the Ball?
There’s clearly many components at play in a Roulette wheel’s construction process, but what would the valuable piece of hardware be without the ball that makes it tick? Well, surprisingly enough, the first Roulette wheels used balls made of ivory bone or wood. However, because these materials can easily scratch or damage the wheel’s finish, today’s Roulette croupiers use nylon or phenolic balls not made by real ivory. The size of the ball varies depending on the wheel’s diameter and pocket width, although a ball between 18mm and 21mm is the most common.
Roulette Wheel Post-Construction Testing
As is the case with most newly manufactured products, testing is the final stage before shipping. The same is true with the Roulette wheel, as it must undergo quality tests to ensure things like spin velocity and ease, pocket size, and more. Mechanical imperfections can alter gameplay in big ways, so it’s best to eliminate them before the wheels hit casino floors.
Roulette Wheel and the Digital Age
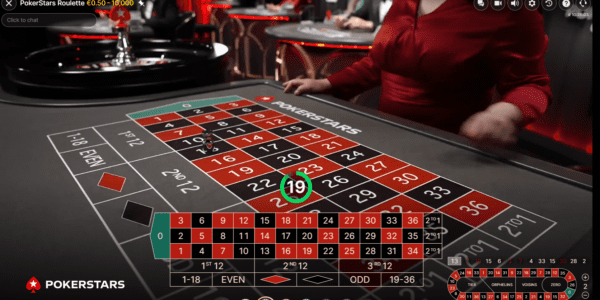
The advent of the internet meant that certain games and other types of entertainment would become obsolete. Not so for this 18th-century game. No, it evolved with the times and was actually one of the very first online casino games that was made available to players at online casino sites.
These days, the market for different types of roulette games online has grown tremendously. Some of the more popular roulette titles include Multi-wheel roulette, Lightning roulette, Double Ball roulette and Mini roulette. The variety of roulette games available shows the interest among roulette players, and game developers are constantly creating new and improved versions to appeal to every taste.
In the digital age, this is done by making live streaming and virtual roulette games possible. The new online roulette games have a foundation that may stay true to the original, however, some unique and interesting features can only be found at online casinos due to technological advancements. These include nifty side bet options, more efficient ways of players, and immersive experiences with live dealers, virtual reality, and augmented reality.
Roulette and RNG
One of the main concerns when roulette appeared online was how could players be sure that the game was conducted in a fair manner. Could game developers recreate the randomness that occurs when the ball spins around the track before it falls into its fated slot? The answer to this question was the creation of RNG or a Random Number Generator. The technology behind this sophisticated software algorithm means that every spin of the roulette wheel is unpredictable and independent.
How does RNG Work?
How the technology works can be explained simply, although it is anything but that. The RNG produces a significant amount of random numbers on a continuous basis. These are all numbers that represent potential outcomes, as is where the ball could land next on the roulette wheel. When players “spin” the wheel online, the game will choose one of these random numbers that have been generated. The selected number is then chosen, and it could be red, black, odd, or even. This means that players (and even the casino itself), have no way of spotting a sequence or determining which number will be chosen next.
Another aspect that ensures true randomness, fairness, and reliability is that these RNGs are constantly tested and certified by independent auditing agencies. Now, online casinos can create a truly authentic roulette experience that is immersive for players.
Roulette’s Tech Developments
The mechanics of roulette and how it was played generally stayed the same until it moved online. For example, wheels were spun manually by the croupier before the discovery of electricity, which could then keep the wheels spinning all the time.
Technologically, roulette developed greatly once it became available online. There was the introduction of RNG, followed by the variants that provided different side options and bets. An example of a different type of roulette only available online is Lightning Roulette. In this game, lightning will strike random numbers and if a player has placed a bet on one of these, then the stake payout is multiplied.
Live streaming is another key development in roulette online. This is where dealers will occupy studios that have a roulette wheel and the entire game set up. The dealer will play the game and engage with the players as if they were at a real land-based casino. This creates a feeling of the more traditional game, where players can interact with the dealer and with each other, and it is one of the most popular types of roulette played online today.
Major technological advancements have allowed Roulette and many other casino games to be digitized, taking the process of wheel construction completely online, as providers employ graphic designers over manufacturing companies. Although this may be the future of Roulette gaming, it’s interesting to see how each piece still comes perfectly together nowadays to form that same wheel that was first thought up hundreds of years ago.